Sheet metal manufacturing is the basic guarantee for enhancing market competitiveness and reliability. However, sharp outer edges or burrs are often created during the manufacturing process, which can cause a series of problems in later production and processing applications. Therefore, it seems particularly important to eliminate this defect quickly and neatly, a sheet metal deburring machine can help you to handle these tasks. Today, we will take you to gradually grasp the characteristics of sheet metal deburring equipment and help you choose a suitable sheet Metal Deburring Machine.
Burrs are inevitable
The first thing to be clear is that sharp edges, burrs and residues are inevitable in the production, which are mainly derivatives of cutting processes such as laser cutting and flame cutting. These flaws also hinder a smooth and fast machining process. Sharp burrs also increase the risk of personal injury, that’s why we have to deburr metal plates and parts after cutting. You can quickly get the ideal machining parts using a sheet metal deburring machine.
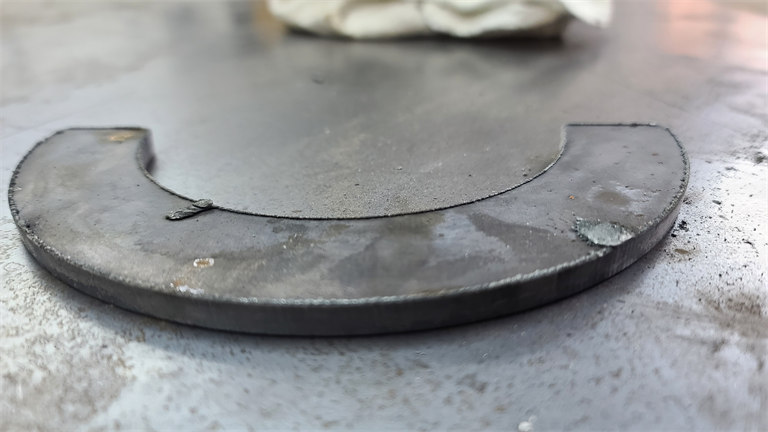
Currently there are many traditional deburring methods. The basics are manual deburring, which is removed by a skilled worker using a brush or angle grinder, it is time-consuming and impossible to guarantee a consistent result, the final processing effect depends on the skill and experience of the operator. Another option is to use a vibration type deburring machine which is more suitable for smaller parts. After the sheet metal parts to be processed (such as small flame-cut parts) are placed in the drum together with the abrasive and rolled for a while, the burrs can be removed and the sharp edges will be passivated. However, it is not suitable for large parts yet some workpieces cannot be rounded. If you need to deburr large batches or large sheets, then it’s a wise choice purchasing a CNC deburring machine. There are a variety of deburring machines available for different usages, here are some recommendations when you are choosing a right model:
1.The workpiece quantity
It’s more valuable to own a deburring machine if your need to process large amount workpieces. When processing large batches, it is especially important for time and cost savings, these two factors play a crucial role in the whole profitability. Based on experience, a worker operating a sheet metal deburring machine can get at least four times efficiently than a traditional manual process, this is a criterion to consider whether to invest in a deburring machine. In addition to the reduction in labor cost, several other aspects have a positive impact: First, occupational safety is significantly improved since the deburring machine eliminates the risk of injury caused by hand tools. Second, the working environment becomes cleaner because the machine recycles all the grinding dust centrally. You’ll be surprised how economical a sheet metal deburring machine can be If you calculate the total cost and combine with the productivity gains.
Companies that produce high-volume and diverse sheet metal parts require consistently high-precision parts. These factors are critical for downstream manufacturing to meet customer needs. For high requirements workpieces, it’s necessary to invest in a CNC sheet metal deburring machine. In addition, a deburring machine can quickly adapt to different machining tasks by activating or deactivating one machining unit. When processing large batches of parts, you can easily apply to a large-volume processing mode, this mode should be flexible enough to meet a variety of different edge requirements.
2.Types of processing metal sheets
It’s a key point of the final processing effect needs to be achieved before choosing a suitable machine. When you are looking for a metal deburring machine, you need to be clear about the workpieces and the edge processing requirements. The model selected needs to cover the main product range with high quality and low cost.
For example, CNC metal deburring machine is a proven and cost-effective way to process flame-cut parts. Even though there are limitations in small size workpieces, but it’s an economical option for flame-cut parts surface finishing. Instead, we need to consider how often “exceptions” occur. This is how to focus on effective procedures when dealing with main business.
It’s quite different for laser-cutting parts. Ideally, you should choose a solution that covers the full range of laser cut parts, especially for different thickness. However, there are also questions: What are the edges rounding requirements? How about the consistency? Or is processing speed more important? Make sure you take into account customer requirements as well as your processing chain.
The sheet metal processing chain is always an important factor influencing cost efficiency. Consider the cost of sheet metal deburring machines as a whole, you can compare with other processing steps and create detailed cost-benefit calculations, this is a key part in financial efficiency.
The selection criteria also include lead time, cost-effectiveness, technology and the quantity and characteristics of the metal plates. Obviously you will definitely find a suitable machine following these suggestions.